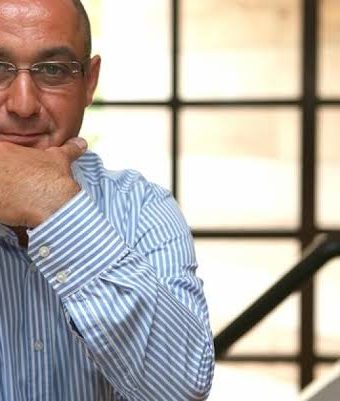
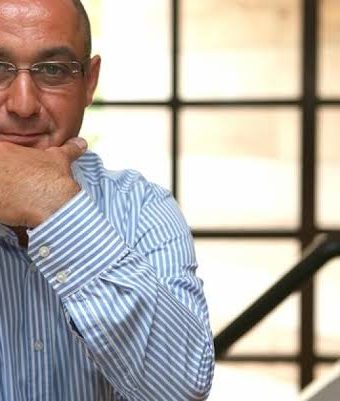
Přejít k obsahu | Přejít k hlavnímu menu | Přejít k vyhledávání
You must have heard it a hundred times. Modern production is agile, flexible, automated, lean, built on technologies, using the possibilities of artificial intelligence. These are all beautiful, soaring words. But of course, putting them into practice is not just that. Especially when you have been building a really wide portfolio of products for more than 25 years and you have been supplying them in hundreds of countries to hundreds of countries around the world over the years.
Your field is constantly changing, some machines are aging and some people are working with them. Nevertheless, Petr Demek, head of production at ELKO EP – the European leader in the production of relays and intelligent wiring – is fundamentally convinced that a bet on development and production under one roof is the absolute best possible option for success. “Production is a struggle on three fronts and you must not lose on either. The first is for a customer who wants a quality and cheap product. You wage the second battle for the workers who create that value and spend a third of their lives in the work environment. And the third is the benefit to the company itself, which relies heavily on a successful fight in the first two, “he describes at the beginning of his story.
What measures are you taking to speed up and streamline production?
Much of it is hidden in the processes and machinery themselves. But that is more of a result. What doesn’t pay enough attention is that in order for everything to happen, you have to have the main thing. Build a functional team. There I see the Achilles heel of all efficiency solutions. It is forgotten that it is the team that must effectively cover the competencies in order to be able to implement all projects. There is no room for modern accumulated production of Ferda the Ants and their daily graduation. Their mistakes cost considerable resources. Once you have a functional specialized team, you can better map inefficient areas of the production process and you can also solve potential problems.
What “drives forward” and what are its relationships?
I don’t want to shout at anything here. It is team work, with various joys and sorrows, but I am convinced that we are working very well. This is also proved by the low fluctuation in THP production positions. We are all driven forward by change, our goal and successful sub-goals, in turn, support motivation.
What do you personally enjoy most about work?
The ability to make meaningful changes.
How many people are currently working in production? And what are the expectations for the future?
At present, the production and quality department has 117 employees. For THP employees, I plan to restructure the departments in order to achieve the highest possible efficiency and thus keep in progress all planned and implemented changes, which should ultimately create benefits primarily for our customers and are a prerequisite for some looming strategic collaborations. This will bring staff reinforcement.
Strengthening? One would expect the opposite process in automation.
In practice, this is not how it works at all. Our goal is to transfer workers to the roles of machine operators or to higher funded manual operations with high added value, where machines and man’s precision are very difficult to replace. We carry out this process in such a way that those new technologies and optimized product designs (for machines or manual work) meet at the appropriate time with the creation of line capacity, which these workers will subsequently strengthen. Although most employees will merge into a few manual work activities over time, we are constantly working to maintain the growth trend, thus intending to use these capacities.
Do you think that production and development under one roof, in the Czech Republic, are the right prerequisites for the future success or competitiveness of the company?
The topic itself is so complex that it would publish the article itself. I will therefore answer briefly. From the point of view of geography, it is definitely more advantageous if there are both the development department and the production preparation and the production itself physically in one area. This allows all matters to be resolved immediately, on the spot and with the participation of all those who can realistically contribute to the solution. The second view is organizational. In small to medium-sized companies, it is 100% better when production and development is organizationally under one roof. You can still set up such companies on an operational basis and with direct communication. Everyone knows each other; they know their competencies, tasks. For larger medium and large companies, this organizational arrangement is completely impossible, and where the transition from that “family” system to a corporate, depersonalized system has failed, the vast majority of companies have stunted. The reason is simple. Coordination of the activities of a large collective can no longer depend on the mutual knowledge of individuals. It is already necessary to control who does what and how in the system, to which you apply a number of metrics for its evaluation. At this stage, you will basically find that the system holds up much better in smaller sub-units. This is the only way to keep the much higher volume of work and, most importantly, the flow of information in the guardrails. So here it is necessary to systematically divide the company into clear divisions, which function in a similar way as separate entities
How do you perceive the future of the product portfolio?
I do not dare to predict the future, from the point of view of production; I would like it to grow in the whole range of product lines. What we strive for every day would be all the more important.